Top 5 Tools and Equipment for ASTM-Compliant Atterberg Testing
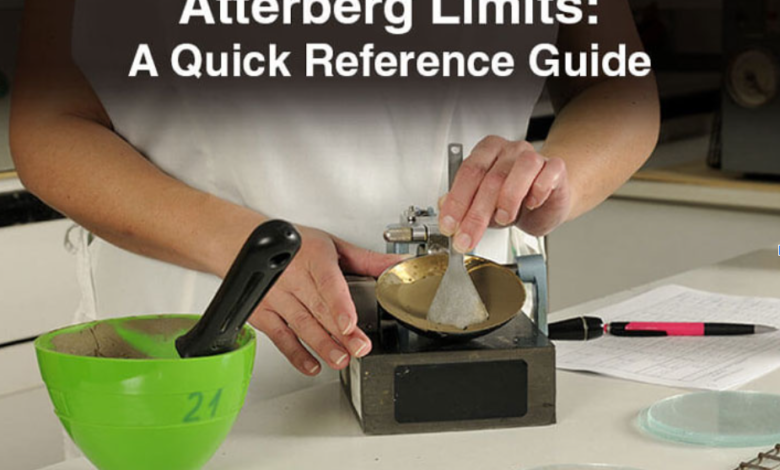
Introduction to Atterberg Limits Testing
Atterberg limits astm represents one of the most fundamental and widely performed geotechnical engineering procedures in soil mechanics laboratories worldwide. Named after Swedish agricultural engineer Albert Mauritz Atterberg, these tests determine the moisture content boundaries at which fine-grained soils transition between different consistency states. The significance of Atterberg limits extends far beyond academic curiosity, forming the backbone of soil classification systems and providing critical insights into soil behavior under various environmental conditions.
The concept of Atterberg limits encompasses three primary boundaries: the liquid limit, plastic limit, and shrinkage limit. These limits define the moisture content thresholds where soil exhibits distinct behavioral characteristics. The liquid limit represents the water content at which soil transitions from a plastic to a liquid state, while the plastic limit marks the boundary between plastic and semi-solid states. The shrinkage limit, though less commonly tested, indicates the moisture content below which further drying does not result in additional volume reduction.
Understanding these limits proves invaluable for engineers working on foundation design, slope stability analysis, pavement construction, and countless other geotechnical applications. The plasticity index, calculated as the difference between liquid and plastic limits, serves as a fundamental parameter in soil classification systems such as the Unified Soil Classification System and AASHTO classification method. This index provides engineers with essential information about soil compressibility, shear strength characteristics, and potential for volume change under varying moisture conditions.
Modern geotechnical practice demands adherence to standardized testing procedures to ensure consistency, reliability, and comparability of results across different laboratories and projects. The American Society for Testing and Materials has developed comprehensive standards that govern every aspect of Atterberg limits testing, from sample preparation through result interpretation. These standards ensure that testing procedures remain consistent regardless of geographic location, laboratory size, or testing personnel experience level.
Understanding ASTM Standards for Atterberg Testing
The ASTM D4318 standard serves as the primary reference document for liquid limit, plastic limit, and plasticity index determination of soils. This comprehensive standard encompasses detailed procedures, equipment specifications, sample preparation requirements, and quality control measures that laboratories must implement to achieve reliable, reproducible results. The standard has undergone numerous revisions since its initial publication, reflecting advances in testing technology, improved understanding of soil behavior, and enhanced quality assurance practices.
ASTM D4318 specifies two alternative methods for liquid limit determination: the multipoint method and the one-point method. The multipoint method, considered the reference procedure, involves testing soil samples at multiple water contents to establish a flow curve, from which the liquid limit is determined at 25 blows using the Casagrande liquid limit device. The one-point method, while faster and requiring less material, provides results that may be less precise under certain conditions, particularly when dealing with unusual soil types or when operator experience is limited.
The standard addresses critical aspects of sample preparation, including air-drying procedures, particle size requirements, and moisture conditioning techniques. Proper sample preparation significantly impacts test reliability, as inadequate preparation can introduce errors that propagate through subsequent testing phases. The standard requires that samples be prepared from soil passing the No. 40 sieve, ensuring that coarse particles do not interfere with the testing process while maintaining representative soil characteristics.
Quality control provisions within ASTM D4318 establish precision and bias requirements that laboratories must meet to demonstrate acceptable testing performance. These requirements include specific tolerances for duplicate testing, calibration verification procedures, and proficiency testing participation. Laboratories seeking accreditation must demonstrate compliance with these quality control measures through documented procedures, regular equipment calibration, and ongoing personnel training programs.
The standard also addresses environmental considerations, including laboratory temperature and humidity controls that can influence test results. Fluctuations in ambient conditions can affect soil moisture content, evaporation rates, and material handling characteristics. Proper environmental controls ensure that testing conditions remain consistent throughout the testing process, minimizing variability introduced by external factors.
Essential Tool 1: Liquid Limit Device (Casagrande Apparatus)
The Casagrande liquid limit device stands as the cornerstone of Atterberg limits testing, representing over a century of evolution in soil testing technology. This precision mechanical instrument determines the liquid limit through a standardized procedure that measures soil flow characteristics under controlled impact conditions. The device consists of a brass cup mounted on a cam-operated mechanism that delivers consistent, repeatable impacts to soil samples placed within the cup.
The fundamental design principle of the Casagrande device centers on delivering a standardized impact energy to soil samples through a precisely controlled dropping mechanism. The brass cup, with its specific dimensions and weight distribution, falls a fixed distance of 10 millimeters onto a hard rubber base through cam-operated lifting and release cycles. This consistent energy input allows for reliable determination of the moisture content at which soil flows together for a distance of 13 millimeters after exactly 25 blows.
Modern Casagrande devices incorporate numerous refinements over the original design, including improved bearing systems, enhanced durability materials, and precision manufacturing tolerances. The cam mechanism must operate smoothly without binding or irregular motion, as any deviation from the specified drop height or impact energy will compromise test accuracy. High-quality devices feature hardened steel cam surfaces, precision-ground bearing surfaces, and robust construction materials capable of withstanding thousands of testing cycles without significant wear.
Calibration of the liquid limit device represents a critical aspect of maintaining testing accuracy and ASTM compliance. The standard requires regular verification of drop height, impact energy, and mechanical components through specific calibration procedures. Drop height verification involves measuring the actual fall distance of the cup using precision gauges or dial indicators, with acceptable tolerances specified in the standard. Any deviation beyond acceptable limits necessitates adjustment or device replacement.
The grooving tool, an integral component of the liquid limit testing procedure, requires equal attention to precision and maintenance. This specialized tool creates the standardized groove in soil samples that serves as the flow measurement reference. The tool dimensions, cutting edge geometry, and handle attachment must conform to specific requirements outlined in ASTM D4318. Regular inspection and replacement of worn grooving tools ensures consistent groove formation and accurate flow measurements.
Proper maintenance of Casagrande devices extends their operational life while maintaining testing accuracy. Regular cleaning removes soil residues that can accumulate in moving parts, potentially affecting mechanical operation. Lubrication of bearing surfaces and cam mechanisms prevents excessive wear while ensuring smooth operation. Storage in controlled environmental conditions protects precision components from corrosion, temperature fluctuations, and physical damage.
Essential Tool 2: Plastic Limit Rolling Device and Glass Plate
The plastic limit determination process relies on specialized equipment designed to facilitate the precise formation of soil threads with standardized dimensions. While the basic concept involves rolling soil samples into threads of specific diameter, achieving consistent, repeatable results requires carefully selected tools that provide appropriate surface characteristics, dimensional control, and ergonomic operation. The rolling surface and associated equipment must meet specific requirements outlined in ASTM D4318 to ensure testing accuracy and operator comfort during extended testing sessions.
The primary rolling surface consists of a ground glass plate with specific surface finish requirements that provide optimal friction characteristics for soil thread formation. The glass surface must be sufficiently rough to prevent soil slipping during rolling operations while maintaining smoothness adequate for consistent thread formation. Surface preparation and maintenance of glass plates directly impact testing reliability, as worn or contaminated surfaces can produce irregular thread formation or inconsistent results.
Alternative rolling surfaces, including specialized plastic or metal plates, have gained acceptance in many laboratories due to their enhanced durability and consistent surface characteristics. These alternative surfaces must demonstrate equivalent performance to ground glass plates through comparative testing and validation procedures. The selection of rolling surface material often depends on laboratory preferences, testing volume, and maintenance considerations, provided that ASTM requirements are met.
The rolling rod, typically constructed from stainless steel or other non-reactive materials, serves as the primary tool for soil thread formation. Rod diameter, surface finish, and weight distribution significantly influence rolling effectiveness and operator fatigue during extended testing sessions. Standard specifications require specific dimensional tolerances and surface characteristics that ensure consistent soil manipulation without introducing variability due to tool irregularities.
Thread diameter measurement represents a critical aspect of plastic limit determination that requires specialized tools for accurate assessment. Various measurement devices, including dial calipers, micrometers, and comparison templates, provide different approaches to dimensional verification. The selection of measurement tools often depends on laboratory preferences, testing volume, and required precision levels, with each approach offering specific advantages and limitations.
Modern plastic limit testing has benefited from the introduction of mechanical rolling devices that provide consistent pressure application and rolling speed control. These devices reduce operator variability while improving testing efficiency and reducing physical demands on laboratory personnel. Mechanical rolling devices typically feature adjustable pressure settings, variable speed controls, and ergonomic designs that accommodate different operator preferences and testing requirements.
Quality control in plastic limit testing extends beyond equipment selection to encompass operator training, procedure standardization, and result verification protocols. Consistent technique development among laboratory personnel ensures that equipment capabilities translate into reliable test results. Regular inter-laboratory comparison testing and proficiency evaluation programs help identify equipment or procedural issues that might affect testing accuracy.
Essential Tool 3: No. 40 Sieve and Sieving Equipment
Sample preparation for Atterberg limits testing requires precise particle size separation to ensure that only appropriate soil fractions undergo testing. The No. 40 sieve, with its 0.425-millimeter opening size, serves as the primary tool for removing oversized particles that could interfere with liquid and plastic limit determinations. Proper sieving equipment selection, maintenance, and operation directly impact the reliability and accuracy of subsequent Atterberg limits testing procedures.
ASTM D4318 specifically requires that Atterberg limits testing be performed on soil fractions passing the No. 40 sieve, recognizing that larger particles can significantly influence test results through mechanical interference rather than representing the plastic behavior of fine-grained soil constituents. The standard establishes specific requirements for sieve construction, opening dimensions, and wire specifications that ensure consistent particle size separation across different laboratories and testing conditions.
High-quality testing sieves incorporate precision-woven wire cloth with exact opening dimensions manufactured to strict tolerances. The sieve frame construction must provide adequate strength and dimensional stability while maintaining proper wire cloth tension throughout extended use periods. Stainless steel wire cloth offers superior durability and corrosion resistance compared to alternative materials, particularly in laboratory environments where moisture and chemical exposure may occur.
Mechanical sieving equipment enhances efficiency and consistency in sample preparation operations, particularly for laboratories processing large numbers of samples. Sieve shakers provide standardized agitation patterns and intensity levels that ensure complete particle separation while preventing wire cloth damage or excessive wear. Variable amplitude and frequency controls allow operators to optimize sieving parameters for different soil types and moisture conditions.
The sieving process itself requires careful attention to technique and timing to ensure complete particle separation without introducing errors. Adequate sample quantities, appropriate sieving duration, and proper washing procedures contribute to accurate particle size separation. Overloading sieves can result in incomplete separation, while excessive sieving duration may cause particle breakdown or wire cloth wear.
Sieve maintenance and calibration represent essential aspects of quality assurance in Atterberg limits testing. Regular inspection of wire cloth condition, opening dimension verification, and frame integrity assessment help identify potential sources of error before they affect test results. Damaged or worn sieves must be replaced promptly to maintain testing accuracy and ASTM compliance.
Washing procedures for sieve cleaning require specific techniques and equipment to remove soil residues without damaging wire cloth or altering opening dimensions. Ultrasonic cleaning systems provide effective soil particle removal while minimizing mechanical stress on sieve components. Proper drying and storage procedures prevent corrosion and maintain sieve condition between uses.
See also: XRP Price Analysis: Why It’s Performing Better Than Expected
Essential Tool 4: Precision Balance and Weighing Equipment
Accurate mass measurements form the foundation of reliable Atterberg limits testing, as these tests fundamentally depend on precise determination of soil moisture content at various consistency states. The selection, calibration, and operation of weighing equipment directly impact the accuracy and precision of liquid limit, plastic limit, and plasticity index determinations. ASTM D4318 establishes specific requirements for balance performance, readability, and environmental considerations that ensure adequate measurement precision for meaningful test results.
Laboratory balances used for Atterberg limits testing must provide sufficient readability and stability to detect small mass changes associated with moisture content variations. The standard typically requires balance readability of 0.01 grams or better, with repeatability and linearity specifications that ensure consistent performance across the full measurement range. These requirements reflect the precision needed to detect subtle moisture content changes that define the boundaries between different soil consistency states.
Modern electronic balances incorporate advanced weighing cell technology, digital signal processing, and environmental compensation features that enhance measurement accuracy and reliability. Load cell designs utilizing electromagnetic force restoration or strain gauge technology provide excellent stability and repeatability characteristics suitable for demanding geotechnical testing applications. Internal calibration systems and automatic adjustment features help maintain accuracy over extended periods while reducing maintenance requirements.
Environmental factors significantly influence balance performance, requiring careful consideration of laboratory conditions and equipment placement. Temperature fluctuations, air currents, vibration, and electromagnetic interference can introduce measurement errors that compromise test reliability. Proper balance installation includes vibration-isolated surfaces, draft protection, and temperature-stable environments that minimize external influences on weighing operations.
Sample container selection and handling procedures impact weighing accuracy through considerations of material stability, moisture retention, and measurement convenience. Aluminum or stainless steel containers provide excellent moisture barrier properties while maintaining dimensional stability under varying temperature conditions. Container weight and size must be appropriate for the balance capacity and readability requirements while providing adequate sample handling convenience.
Calibration verification and maintenance procedures ensure continued balance accuracy and ASTM compliance throughout extended service periods. External calibration masses certified to appropriate accuracy standards provide traceability to national measurement standards while enabling regular verification of balance performance. Documentation of calibration results and maintenance activities supports quality assurance programs and accreditation requirements.
Moisture content calculations require careful attention to significant figures and rounding procedures that reflect the precision limitations of measurement equipment. Proper calculation techniques and result reporting procedures ensure that final values accurately represent the measurement precision achieved during testing. Computer-based data reduction systems can improve calculation accuracy while reducing transcription errors.
Essential Tool #5: Oven and Drying Equipment
Moisture content determination represents the final critical step in Atterberg limits testing, requiring precise temperature control and uniform heating characteristics to ensure accurate and reproducible results. Drying ovens used for geotechnical testing must meet specific performance requirements outlined in ASTM standards, including temperature accuracy, uniformity, and stability specifications that ensure consistent moisture removal without introducing errors through overheating or inadequate drying.
ASTM D4318 specifies drying temperature requirements of 110±5°C for moisture content determination, reflecting the balance between effective moisture removal and prevention of soil constituent alteration. This temperature range ensures complete water removal from soil samples while avoiding chemical changes that could occur at higher temperatures. Oven performance must maintain this temperature range throughout the entire drying chamber, with minimal variation between different shelf positions or chamber locations.
Convection ovens with forced air circulation provide superior temperature uniformity and drying efficiency compared to gravity convection designs. The circulation system must provide adequate air movement to ensure uniform heat distribution while avoiding excessive air velocities that could disturb lightweight soil particles or create temperature fluctuations. Proper air circulation also reduces drying time requirements, improving laboratory efficiency and sample throughput.
Temperature control systems incorporating electronic controllers, precision sensors, and automatic adjustment capabilities ensure stable operation and accurate temperature maintenance. Digital controllers with proportional-integral-derivative control algorithms provide superior temperature stability compared to simple on-off control systems. Multiple temperature sensors distributed throughout the drying chamber enable monitoring of temperature uniformity and identification of potential hot spots or cold zones.
Sample container and placement considerations significantly influence drying effectiveness and result accuracy. Aluminum containers with appropriate surface area-to-depth ratios facilitate efficient moisture removal while preventing sample loss through spillage or container deformation. Proper spacing between containers ensures adequate air circulation around each sample, promoting uniform drying characteristics.
Oven calibration and verification procedures ensure continued temperature accuracy and compliance with ASTM requirements. Certified temperature measurement devices, including calibrated thermometers or electronic temperature sensors, provide traceability to national measurement standards while enabling regular verification of oven performance. Multi-point calibration procedures verify temperature accuracy across the full operating range and throughout the drying chamber volume.
Maintenance procedures for drying ovens encompass cleaning, component inspection, and preventive replacement of wear items such as heating elements, circulation fans, and temperature sensors. Regular maintenance ensures continued reliable operation while preventing equipment failures that could compromise testing schedules or result quality. Documentation of maintenance activities supports quality assurance programs and equipment lifecycle management.
Calibration and Maintenance Requirements
Maintaining ASTM compliance and ensuring reliable test results requires comprehensive calibration and maintenance programs that address all equipment components used in Atterberg limits testing. These programs encompass routine verification procedures, scheduled maintenance activities, and documentation requirements that demonstrate continued equipment performance and regulatory compliance. Effective calibration and maintenance programs prevent equipment-related errors while extending equipment service life and minimizing unexpected failures.
Calibration frequencies and procedures vary among different equipment types, reflecting their relative importance to test accuracy and susceptibility to drift or degradation. Critical equipment such as balances and liquid limit devices typically require more frequent calibration verification compared to ancillary equipment with lower impact on test results. Risk-based approaches to calibration scheduling optimize resource allocation while ensuring adequate quality assurance coverage.
Documentation requirements for calibration and maintenance activities support quality management systems and regulatory compliance while providing historical records for equipment performance trending and lifecycle management decisions. Calibration certificates, maintenance logs, and performance records must be maintained in organized, accessible formats that facilitate audits and accreditation activities. Electronic record-keeping systems can improve documentation efficiency while ensuring data integrity and backup protection.
Training requirements for laboratory personnel encompass equipment operation, calibration procedures, and maintenance activities appropriate to their responsibilities and authorization levels. Competency assessment and ongoing training programs ensure that personnel maintain current knowledge of procedures and requirements while adapting to equipment upgrades or procedural changes. Documentation of training activities and competency assessments supports personnel qualification and quality assurance objectives.
Corrective action procedures address equipment failures, calibration discrepancies, and maintenance issues that could affect test results or laboratory operations. These procedures must include immediate response actions, root cause analysis, corrective measures, and verification of effectiveness. Impact assessment procedures evaluate potential effects on previous test results when equipment problems are identified.
Quality Control and Testing Procedures
Quality control in Atterberg limits testing extends beyond equipment performance to encompass sample handling, testing procedures, data management, and result verification activities. Comprehensive quality control programs ensure that all aspects of the testing process contribute to reliable, accurate results while maintaining consistency between different operators, testing sessions, and laboratory conditions. These programs incorporate preventive measures, process controls, and verification procedures that identify and correct potential sources of error.
Duplicate testing requirements establish minimum precision expectations while providing ongoing assessment of testing consistency and operator performance. ASTM D4318 specifies precision criteria for duplicate determinations that laboratories must meet to demonstrate acceptable testing performance. Regular monitoring of duplicate test results helps identify trends or issues that might indicate procedural problems, equipment degradation, or training needs.
Sample tracking and chain-of-custody procedures ensure that samples maintain their integrity and identification throughout the testing process. Proper sample identification, storage conditions, and handling procedures prevent sample mix-ups, contamination, or deterioration that could compromise test results. Electronic sample management systems can improve tracking accuracy while providing comprehensive records of sample history and testing status.
Data management and calculation verification procedures prevent transcription errors and computational mistakes that could invalidate test results. Automated calculation systems reduce manual error opportunities while providing consistent application of calculation procedures and rounding rules. Regular verification of calculation formulas and software algorithms ensures continued accuracy and compliance with standard requirements.
Proficiency testing participation provides external verification of laboratory performance while identifying potential systematic errors or procedural deviations. Interlaboratory comparison programs evaluate testing consistency across different laboratories while providing feedback on individual laboratory performance relative to peer groups. Results from proficiency testing activities inform training needs and process improvement initiatives.
Cost Considerations and Procurement Guidelines
Equipment procurement for Atterberg limits testing requires careful evaluation of performance requirements, budget constraints, and long-term operational considerations. Initial equipment costs represent only one component of total ownership expenses, with calibration, maintenance, training, and replacement costs contributing significantly to lifecycle expenses. Comprehensive cost analysis should encompass all ownership aspects while ensuring that selected equipment meets performance requirements and regulatory compliance needs.
Performance specifications must balance testing accuracy requirements with cost considerations, recognizing that excessive precision beyond standard requirements may not justify additional expenses. Equipment selection should focus on meeting or slightly exceeding ASTM requirements while providing adequate durability and reliability for anticipated usage levels. Vendor reputation, service support availability, and warranty provisions significantly influence long-term satisfaction and ownership costs.
Procurement timing considerations include equipment lead times, installation requirements, and training schedules that ensure seamless integration into laboratory operations. Budget planning should accommodate not only initial purchase costs but also installation expenses, calibration services, training programs, and initial consumable supplies. Coordinated procurement and implementation schedules minimize operational disruptions while ensuring that all equipment components are available when needed.
Vendor evaluation criteria should encompass technical capabilities, service support, training offerings, and financial stability considerations that influence long-term support availability. References from similar laboratories provide valuable insights into equipment performance, reliability, and vendor support quality under real-world operating conditions. Demonstration programs or trial periods can provide hands-on evaluation opportunities before final procurement decisions.
Maintenance contract and service support options vary significantly among vendors and equipment types, requiring careful evaluation of coverage levels, response times, and cost structures. In-house maintenance capabilities may reduce ongoing costs while providing greater scheduling flexibility, but require adequate training, spare parts inventory, and technical expertise. Hybrid approaches combining in-house routine maintenance with vendor support for major repairs often provide optimal cost-effectiveness.
Common Challenges and Solutions
Atterberg limits testing, despite its apparent simplicity, presents numerous challenges that can affect result accuracy, testing efficiency, and operator satisfaction. Understanding these challenges and implementing appropriate solutions ensures consistent, reliable testing while minimizing frustration and wasted effort. Common challenges encompass equipment issues, procedural difficulties, sample-related problems, and environmental factors that require systematic approaches for effective resolution.
Equipment-related challenges frequently involve calibration drift, mechanical wear, and environmental influences that affect instrument performance. Regular calibration verification and preventive maintenance programs address many equipment issues before they impact test results. Understanding equipment limitations and operating characteristics helps operators recognize potential problems and implement appropriate corrective measures.
Sample preparation challenges often arise from unusual soil characteristics, contamination issues, or inadequate preparation procedures that affect subsequent testing phases. Proper sample evaluation, preparation techniques, and contamination prevention measures minimize these difficulties while ensuring representative test specimens. Training programs should emphasize proper sample handling and preparation techniques that prevent common problems.
Procedural challenges may result from incomplete understanding of standard requirements, inconsistent technique application, or inadequate operator training. Comprehensive training programs, detailed procedure documentation, and regular competency assessment help ensure that operators understand and consistently apply proper testing techniques. Standardized procedures and work instructions reduce variability while providing reference materials for training and troubleshooting.
Environmental challenges include temperature fluctuations, humidity variations, and vibration effects that can influence equipment performance and test results. Proper laboratory design, environmental controls, and equipment placement minimize these influences while providing stable testing conditions. Monitoring systems can alert operators to environmental conditions that might affect testing accuracy.
Future Developments in Atterberg Testing Equipment
Technological advancement continues to influence Atterberg limits testing through improved equipment designs, automation capabilities, and data management systems that enhance testing efficiency and accuracy. Understanding emerging trends and technologies helps laboratories plan for future needs while taking advantage of improvements that can benefit their operations. These developments encompass mechanical improvements, electronic enhancements, and software innovations that address traditional testing limitations.
Automation technologies offer significant potential for reducing operator variability while improving testing efficiency and consistency. Automated liquid limit devices with electronic control systems provide precise, repeatable testing conditions while reducing operator fatigue and training requirements. These systems typically incorporate computerized data collection and analysis capabilities that minimize manual calculation and transcription errors.
Digital measurement systems increasingly replace mechanical measurement tools with electronic sensors and data acquisition capabilities that improve measurement precision and data management. Electronic balances with direct computer interfaces eliminate transcription errors while providing enhanced data logging and analysis capabilities. Digital temperature monitoring and control systems ensure precise oven operation while documenting temperature history throughout drying cycles.
Software developments encompass comprehensive laboratory information management systems that integrate all aspects of Atterberg limits testing from sample receipt through final reporting. These systems provide sample tracking, automatic calculation, quality control monitoring, and report generation capabilities that improve efficiency while reducing error opportunities. Integration with other laboratory systems enables comprehensive project management and data analysis capabilities.
Sensor technology advancements may eventually enable real-time monitoring of soil consistency changes during testing procedures, providing enhanced understanding of soil behavior while improving test precision. Miniaturized sensors and wireless communication capabilities could revolutionize traditional testing approaches while maintaining or improving result accuracy.
Certified Material Testing Products (Certified MTP) is a leading supplier of construction materials testing equipment and laboratory supplies in the United States. They offer a comprehensive range of products for testing concrete, asphalt, aggregate, soil, and cement, catering to both field and laboratory applications But no matter whether they are prefered or not, the whole idea behind these tools is similar: getting a polished, shiny, and permanent effect. New to stucco or a seasoned pro, investing in good tools and learning the nuances of their use is what will get you started perfecting your craft.
Frequently Asked Questions
What is the difference between ASTM D4318 multipoint and one-point liquid limit methods?
The multipoint method requires testing soil samples at multiple moisture contents to establish a complete flow curve, from which the liquid limit is determined graphically at 25 blows. This method provides more comprehensive information about soil flow characteristics and is considered the reference procedure. The one-point method uses a single test point with mathematical correction to estimate the liquid limit, requiring less time and material but potentially sacrificing some accuracy, particularly with unusual soil types.
How often should liquid limit devices be calibrated?
ASTM D4318 does not specify exact calibration frequencies, but most quality assurance programs require monthly or quarterly verification of drop height and mechanical components. Daily operational checks should verify proper mechanical operation, while formal calibration should be performed whenever equipment is moved, after major maintenance, or when quality control results suggest potential problems.
What factors affect the accuracy of plastic limit determinations?
Several factors influence plastic limit accuracy, including operator technique consistency, rolling surface condition, thread diameter measurement precision, and environmental conditions such as temperature and humidity. Proper training, standardized procedures, and appropriate equipment maintenance are essential for reliable results. Thread formation technique, including rolling pressure and speed, significantly affects result consistency.
Can alternative drying methods replace standard oven drying for moisture content determination?
ASTM D4318 specifically requires oven drying at 110±5°C for official test results. Microwave drying or other alternative methods may be used for preliminary moisture content estimation but cannot substitute for standard procedures in formal testing programs. Alternative methods may be acceptable for internal quality control or preliminary screening applications with appropriate correlation studies.
What precision requirements must laboratories meet for Atterberg limits testing?
ASTM D4318 establishes specific precision criteria for duplicate testing that laboratories must meet to demonstrate acceptable performance. These criteria vary slightly depending on the soil plasticity level but generally require duplicate results to agree within specific percentages of the average value. Laboratories should monitor duplicate test precision continuously to ensure continued compliance.
How should equipment be stored and maintained between testing periods?
Proper storage involves cleaning all equipment to remove soil residues, protecting metal surfaces from corrosion, and storing in controlled environmental conditions. Liquid limit devices should be covered to prevent dust accumulation and stored where mechanical components are protected from damage. Balances require stable, vibration-free storage locations with draft protection. Regular maintenance schedules should continue even during periods of limited use.
What training requirements exist for personnel performing Atterberg limits testing?
While ASTM D4318 does not specify formal training requirements, laboratory accreditation programs typically require demonstrated competency through training documentation, supervised practice periods, and performance evaluation. Personnel should understand standard procedures, equipment operation, quality control requirements, and safety considerations. Ongoing training ensures continued competency and awareness of procedural updates.
How do environmental conditions affect Atterberg limits test results?
Temperature and humidity variations can affect soil moisture content, equipment performance, and material handling characteristics. Significant temperature changes during testing can alter soil consistency, while high humidity can affect drying rates and moisture loss during sample handling. Laboratory environmental controls should maintain stable conditions throughout testing procedures.
What documentation is required for ASTM compliance?
Comprehensive documentation includes equipment calibration records, maintenance logs, training records, quality control data, and test result documentation. Each test should be documented with sufficient detail to enable result verification and troubleshooting if questions arise. Electronic data management systems can improve documentation efficiency while ensuring data integrity and backup protection.
How can laboratories troubleshoot inconsistent test results?
Systematic troubleshooting should examine equipment performance, procedural compliance, sample characteristics, and environmental conditions. Quality control charts can help identify trends or sudden changes in performance that suggest specific problems. Comparison with reference materials or proficiency testing samples can help isolate the source of inconsistencies. Regular equipment verification and operator training assessment are essential preventive measures.
Conclusion
The successful implementation of ASTM-compliant Atterberg limits testing depends fundamentally on the selection, maintenance, and proper operation of appropriate equipment and tools. The five essential categories of equipment discussed in this comprehensive guide represent the foundation for reliable, accurate testing that meets both regulatory requirements and engineering needs. From the precision Casagrande liquid limit device through specialized drying ovens, each component plays a critical role in ensuring test validity and result reliability.
The investment in quality equipment, comprehensive training programs, and effective maintenance procedures pays dividends through improved testing accuracy, enhanced laboratory efficiency, and reduced long-term operational costs. Understanding the relationship between equipment performance and test reliability enables informed procurement decisions while supporting effective quality management programs. The integration of modern technology with traditional testing principles continues to advance the field while maintaining the fundamental accuracy and reliability that geotechnical engineering demands.
As geotechnical engineering projects become increasingly complex and demanding, the importance of reliable Atterberg limits testing continues to grow. The foundation provided by proper equipment selection and maintenance ensures that laboratories can meet these challenges while providing the accurate, dependable results that support safe, effective engineering design. The ongoing evolution of testing technology promises continued improvements in efficiency and accuracy, but the fundamental principles of careful equipment selection, proper maintenance, and skilled operation remain constant.
Success in Atterberg limits testing ultimately depends on the integration of appropriate equipment, comprehensive procedures, and skilled personnel working together toward the common goal of reliable, accurate results. For more Any Business Card, check out this guide from NFC Business Card The guidelines and information presented in this comprehensive guide provide the foundation for achieving this success while maintaining compliance with ASTM standards and meeting the demanding requirements of modern geotechnical engineering practice.